Александр Жилин. Северские сталеплавильщики убирают свой углеродный след
Экспериментальный проект инженера отдела главного металлурга СТЗ Александра Жилина позволил увеличить работоспособность сталеплавильной печи до 2500 плавок и сократил потребление угля на 40%. 88 миллионов 80 тысяч 400 рублей – экономический эффект реализованного проекта
В семье слесаря-ремонтника ТЭСЦ‑2 СТЗ Михаила Жилина росли три сына. Старший стал энергетиком, средний – строителем, поэтому продолжить заводскую династию Жилиных выпало младшему, Александру.
Школьный журналист
Одни из ярких воспоминаний детства – это время, проводимое каждое лето большой дружной компанией из семей Жилиных, Трушковых, Пятуниных, Ширениных и других в деревне Кенчурке. Свежий воздух, парное молоко, речка, лес – всё в распоряжении детей. «Главное, чтобы картошка была прополота, а остальное время ваше»,– говорили старшие. Небольшой штрих — огороды в деревне большие, но это лишь добавляло азарта мальчишкам.
В школе Александр года три участвовал в выпуске газеты «Готов!», участвовал в выездных сборах актива городской детской организации «Солнечная», был поощрён путёвкой в лагерь «Орлёнок». Детская любознательность подкрепилась творчеством, активной общественной работой. Есть у Александра и вожатский опыт.
Иду в УПИ
Надо сказать, что в жизни ему выпало немало испытаний. Как правило, так говорят о людях солидного возраста, но не в случае с Александром. Ему и его ровесникам выпало стать пионерами в сдаче пробного ЕГЭ. Он вполне успешно справился. Сертификат с необходимым количеством набранных баллов давал право без экзаменов поступить в лесотехнический институт, но Жилин решил по-другому.
«Где родился, там и пригодился» — вооружившись этой пословицей, Александр подал документы в УПИ. В приёмной комиссии был Сергей Петрович Бурмасов. Он, узнав, что прошедший все вступительные испытания Жилин — полевской парень, сразу пригласил его на металлургический факультет. С тех пор Бурмасов стал для Александра не только преподавателем, но и наставником.
Учиться было интересно, но сложно. Александр поступил в тот год, когда полевским уже не давали общежитие, снимать жильё было дорого, приходилось каждый день ездить на учёбу. Вставал в четыре утра и на первый, студенческий, рейс в 5:20 уезжал. Вы помните такую картину: досыпающие в автобусе парни и девчонки? Студенты умели спать стоя, держась за поручни и друг за друга.
Старт карьеры в Уралмаше
Первую практику студент Жилин проходил в ЭСПЦ СТЗ, на участке внепечной обработки стали, вторую, а также преддипломную практики – в металлургической лаборатории НИЦ СТЗ. Получив в июне диплом, Александр Жилин отправился за другим документом – свидетельством о браке. Для свадьбы молодые выбрали красивую дату – 08.08.2008.
Регистрация проходила в музее изобразительных искусств в Екатеринбурге, была очень красивой. А лександр устроился на Уралмаш, работал в должности инженера в отделе главного металлурга. Зарплата была очень достойной. Казалось бы, живи и радуйся. Но грянул экономический кризис – сокращённая рабочая неделя, зарплата упала в два раза. Из-за этого и других несчастий на семейном совете было решено переехать в Полевской.
Домой, на СТЗ и сразу в «пускачи»
Устроиться на Северский трубный завод в 2008 году было практически невозможно, тем более в мартен. Александр Жилин обратился тогда к старшим мастерам: Александру Белёву и Вячеславу Мелингу. Тогда была создана рабочая группа для строительства вакууматора, нужен был инженер. И Александр стал работать в составе «пускачей» под руководством Бориса Глазырина.
– Работать было интересно. Общались со специалистами на смешанном англо-русско-итальянском,– вспоминает Александр.
Конечно, новая работа требовала погружения. Особенно напряжённым был этап гарантийных испытаний, когда всем приходилось задерживаться до поздней ночи. Особенно памятна февральская ночь перед подписанием акта приёмки-сдачи, когда температура опустилась до минус 47 градусов:
– Все в цехе в тёплых куртках, красные от холода, руки не гнутся. Забегали на несколько минут в кабинет, чтобы погреться, и обратно в цех.
Александру Жилину дорого общее фото тех, с кем он работал в составе той пусковой группы. После постройки вакууматора встала новая проблема – утилизация отходов сталеплавильного производства. Александр с коллегами выступили с различными инициативными решениями этой экологической задачи для СТЗ. Вскоре была создана ещё одна рабочая группа. Однако решение было найдено службой экологии в консервативном направлении, не такое по-инженерному красивое, но решавшее проблему на ближайшие 50 лет.
Дед Александра Жилина работал в мартене СТЗ каменщиком-огнеупорщиком, а ещё был очень хорошим печником. Кстати, дедушка и бабушка жили на улице Жилина, Героя Советского Союза, однофамильца. В половине домов улицы Жилина печи были сложены руками Николая Жилина.
Так случилось, что младшему Жилину выпало подхватить печное дело деда. Он тоже помогает работать сталеплавильной печи, правда, не руками, как его дед, который, взяв пару кирпичей и вылив на себя пару вёдер воды, лез в 800-градусное пекло для «горячего» ремонта изношенного места мартеновской печи, но силой инженерной мысли и научных изысканий
Есть над чем голову поломать
Отдел главного металлурга, где трудится Александр, занимается решением возможных технологических проблем, ведь у производственников хватает организационных сложностей, и в приоритете – выпуск продукции. Хотя в отделе есть разделение на группы (Александр возглавляет группу по огнеупорам), каждый из специалистов знает те задачи, над которыми бьются коллеги. Зачастую приходится сообща искать подходы к решению той или иной проблемы. Чтобы получить необходимые недостающие данные, сотрудничают с металлургическим факультетом УрФУ, лабораторией НИЦ СТЗ.
Для Александра проблемы – это возможность в хорошем смысле поломать голову, ему интересны научно-производственные задачи, процесс поиска решения. А результат приносит удовольствие. Это как в детстве, признаётся он, любопытно же разгадать ребус или загадку. Ведь в основе его работы – творчество.
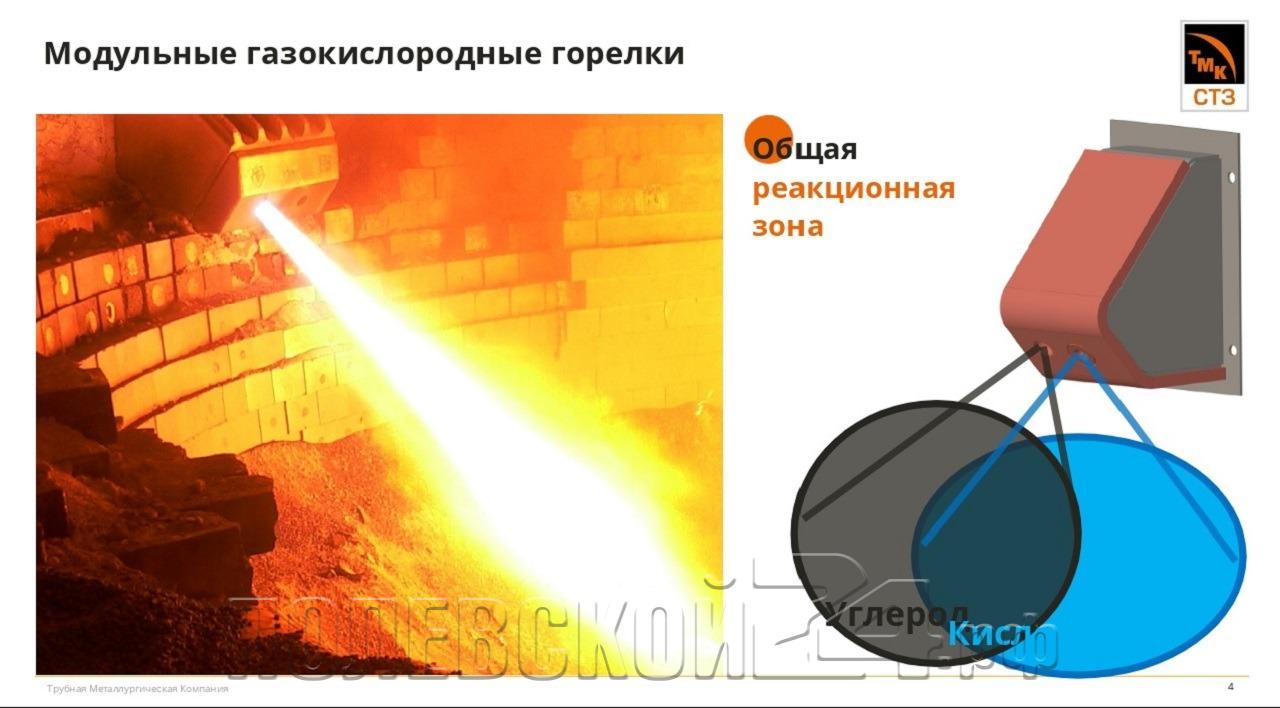
Как вспенить шлак и сохранить футеровку
Проблема для темы, с которой Александр Жилин выступил на последней международной МНПК в Сочи, возникла ещё на ранних этапах освоения ДСП. Тогда исходили из тех ресурсов и возможностей, что были. До недавнего времени проблему удавалось решать технологическими приёмами, и довольно неплохо. Но она требовала кардинального решения – установки в печи модульных газокислородных горелок и инжектора для вдувания в печь углеродной пыли с одновременным её окислением подаваемым кислородом для получения надёжно вспененного шлака.
Требовалось не просто вспенить шлак и закрыть тем самым электрические дуги, чтобы энергия шла на плавление шихты, повысить тепловой КПД электропечи, но и снять тепловую нагрузку с защитных огнеупорных элементов внутреннего пространства печи – футеровки, свода.
До модернизации горелок сталеплавильщики вынуждены были идти на перерасход угля, заставляя вспениваться шлак, окисляя углерод, растворяемый в жидком металле, так как существующие горелки, подающие кислород, и инжекторы, вдувающие угольную пыль, были расположены в печи достаточно далеко друг от друга.
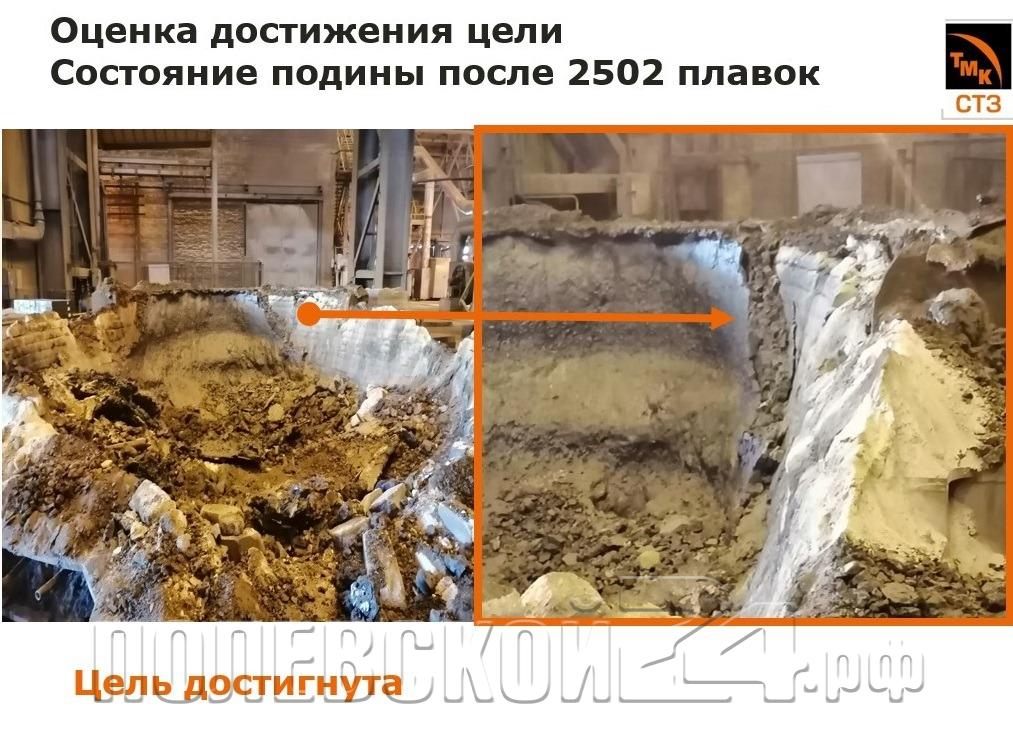
Как рассказал Александр, похожий доклад в Сочи представил и Таганрог. Но к результату СТЗ – 2500 плавок в одной печи – приблизиться никто из коллег с других заводов не смог. Победа проекта Александра Жилина в сталеплавильной секции на «Горизонтах» была логичной. Более того, Северский трубный завод стал одним из первых заводов ТМК, кто реально поддерживает тренд в мировой экологии – снижение углеродного следа.
Личный зачёт Александра Жилина в МНПК СТЗ – ТМК:
2012 год – 1 место.
2015 год – 1 место.
2016 год – 2 место.
2021 год – 1 место.
Вечный студент Высшей школы производства
Александр Жилин, в этом году участвовавший в МНПК уже в 10-й раз, готов передать эстафету участия в «Горизонтах» своим коллегам. Он переходит в статус наставника. По его мнению, формат МНПК давно перешёл из индивидуальной борьбы в командную. Ведь командные проекты дают наибольший результат. Александр по-прежнему много читает (в его телефоне сейчас электронные книги «Разумный инвестор» и «Планирование экспериментов»), учится – физическая химия его «вечный предмет».
Внимательно следит за новинками в теме экологии, изучает новые методы статистики и аналитики. В его рюкзаке – различные материалы для проектной деятельности. Со стороны взглянуть, ни дать ни взять студент Высшей школы производства под названием Северский трубный завод.
Александр – любящий и заботливый муж и отец 11-летней дочки и 4-летнего сына.
– Позитив нельзя терять, если запал иссяк, нужно искать поводы для позитива. Развиваться, радоваться жизни, общаться с близкими, с друзьями,– такой совет даёт себе и читателям Александр Жилин.
Ирина Григорьева
Спасибо!
Теперь редакторы в курсе.